Last year was stressful for the manufacturing industry indeed. The pandemic resulted in so many shifts in the supply chain, and there is higher pressure for it to meet up with demands.
This crisis has changed how industries like manufacturing work. In a Salesforce research, 66% of their respondents from salespeople in manufacturing, energy, and utilities said they’ve taken on new responsibilities in their role. 72% of these sales reps also answered that their success metrics changed and 75% had to adjust to new ways of selling quickly.
A recent report from Fictiv revealed that 95% said that the pandemic had long-term effects on their business. The respondents (with that same amount) also agreed that digital transformation is essential to their company’s success in the future. It also showed that 91% mentioned that they increased investments in digital transformation during the past year.
However, there were a lot of challenges that this industry experienced. The same study also stated that around 44% experienced difficulty recruiting manufacturing talent with essential digital expertise. Another hurdle is how unchangeable supply chains avoid progress. In the survey, 94% of respondents reported concerns about their company’s existing supply chain. Now, that’s a lot!
But despite the obstacles, this industry is already jumping back on track with digital transformation focused on being resilient, enhancing speed, and even considering sustainability. As we can observe in the pandemic, technology is always part of every field of work.
Having technological solutions went from being optional to a necessity for businesses. So what are this year’s tech trends that helped this industry strive? Luckily, Professor 3P is here to answer that question for today’s class.
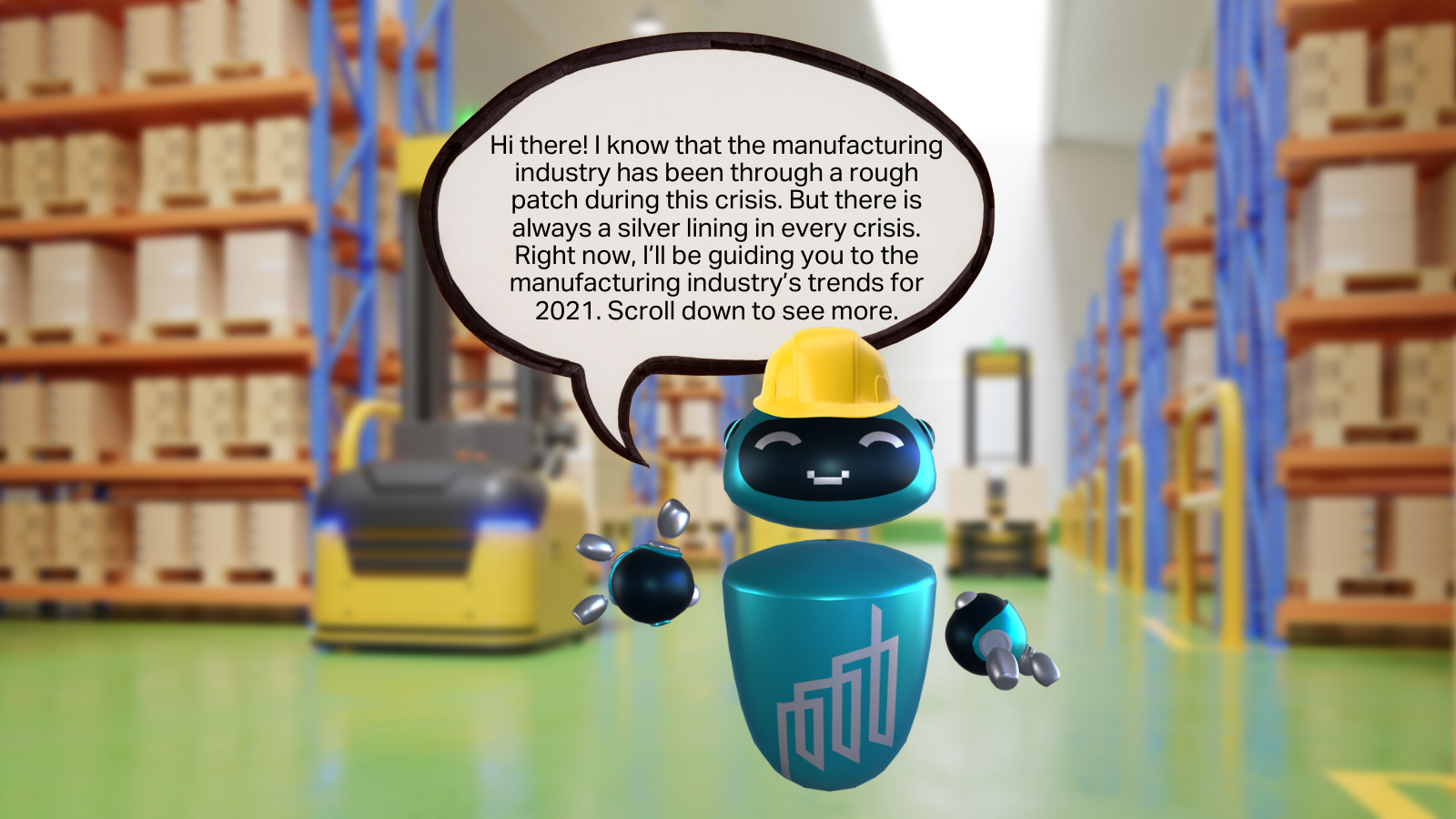
Software solutions
Organizations need information technology (IT) solutions that accelerate digital transformation and are ready for tomorrow’s market. It is crucial to have this infrastructure so that the supply chain data is secured.
For example, there are customer relationship management (CRM) solutions like Salesforce Manufacturing Cloud. You can get a complete view of your customer or clients throughout all channels with this platform! This feature will help your team provide personalized services, lead generations, and engage with customers anywhere.
Better communication methods
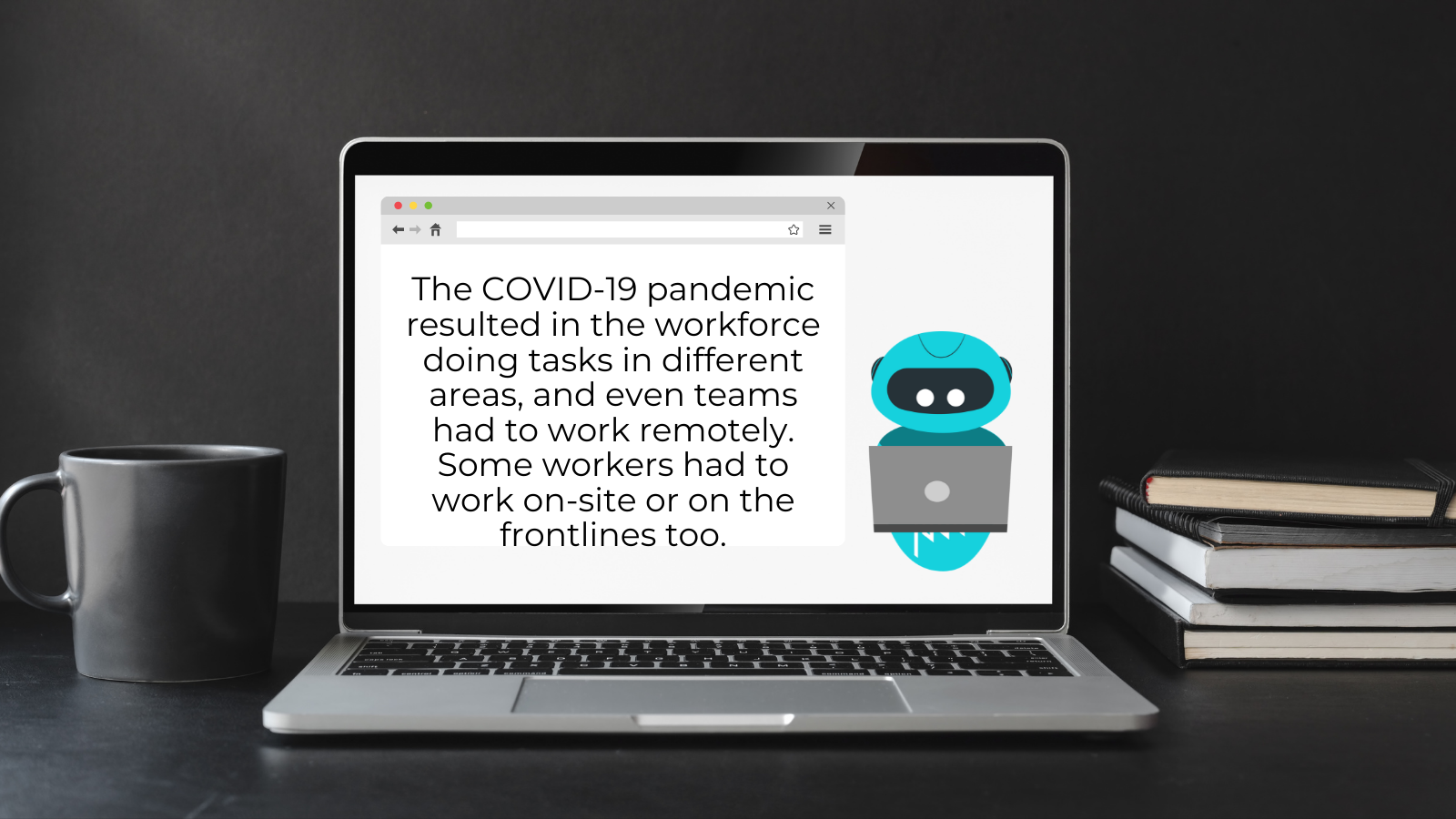
An article revealed that 60% of companies are motivated to have digital tools to centralize communication. Businesses had to find a way to contact everyone on one platform to maintain or increase worker productivity and coordination. There are even manufacturing industries that operate sensitively.
One of the solutions is communication platforms and mobile productivity tools! What I recommend to you is Salesforce Employee Experience. Not only does this software give you a 360-degree view of your employees, but it also helps keep them engaged through personalized communication all in one central feature. They can have access to this platform via mobile wherever they are.
3D Printing to produce products
This tool has been part of manufacturing ever since before, and now, it has become more popular and innovative. I’m sure that you’ve heard the stories of how people use 3D printing to save lives, such as individuals making prosthetic arms through using this tool.
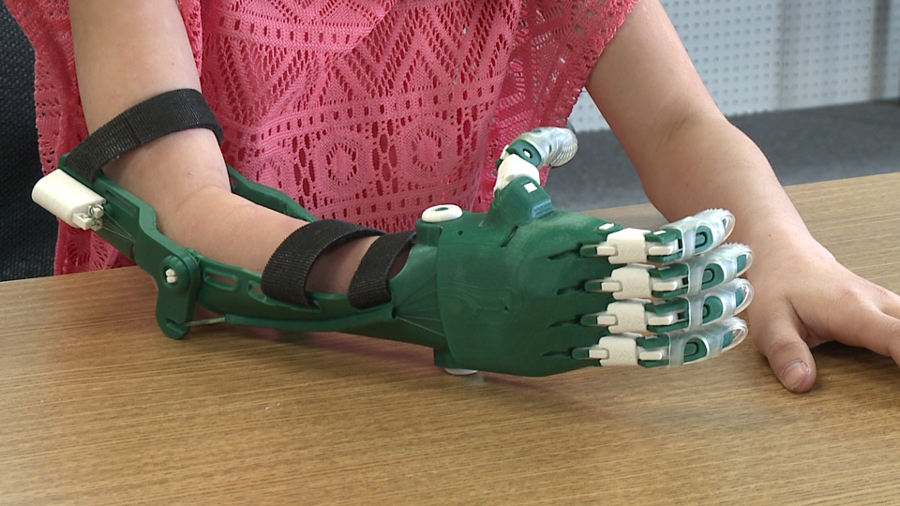
For this industry, manufacturers rely on 3D printing, a highly cost-effective trend, to support creating a product. It lets product designers test and troubleshoots their ideas into life. What makes it convenient is that it can avoid the hassle of manufacturing and warehousing the product concepts.
It has changed the time-consuming process of creating tools. There is no need for your manufacturers to go through lengthy tasks or depend on tooling companies from other countries. To see the first product appeal, they can just use a 3D printer.
Sustainability
This industry has an impact on energy consumption and global emissions. No wonder that there is a need for manufacturing to become more sustainable and eco-friendly.
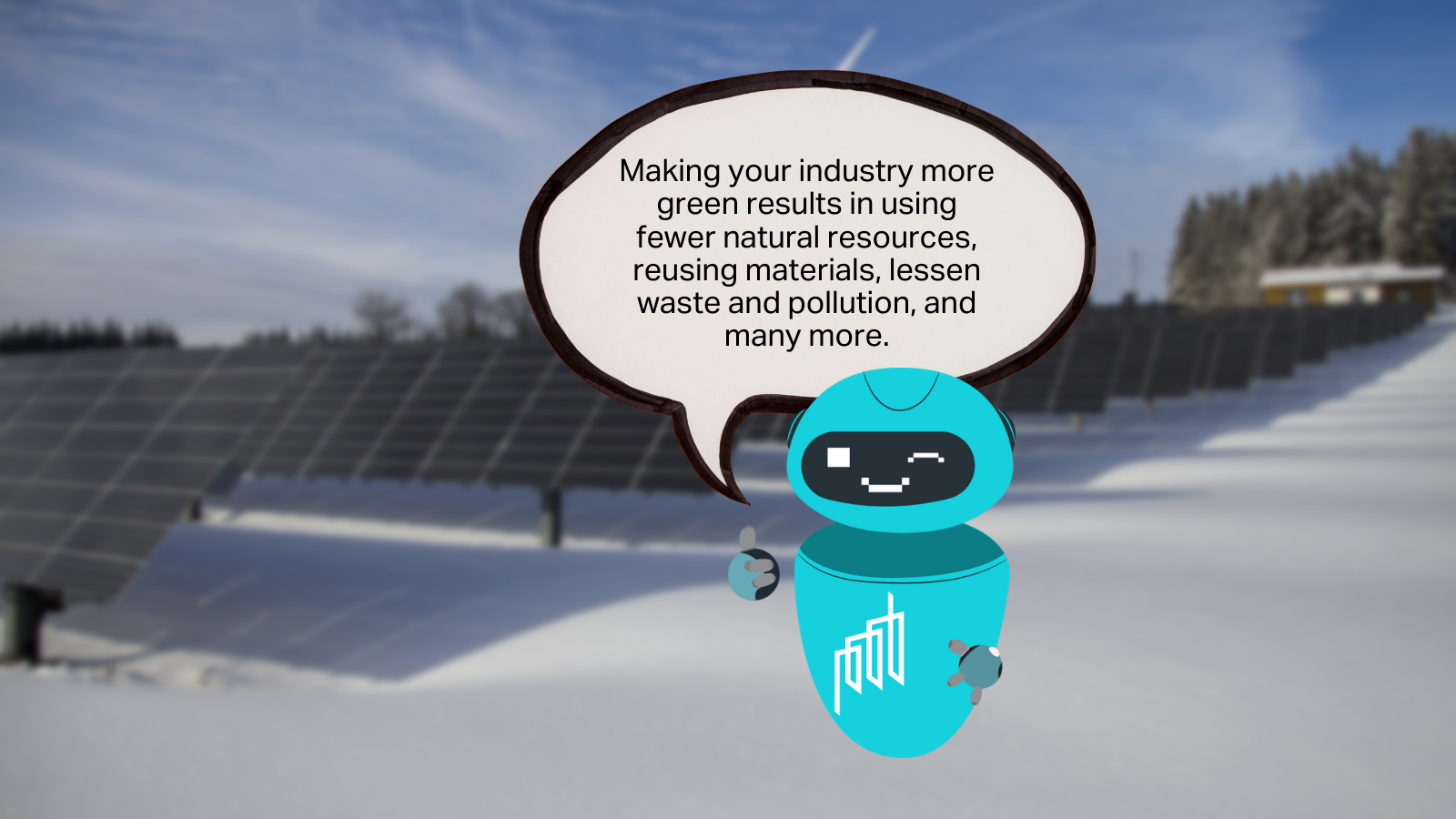
The demand for the global green building materials market is increasing this year. According to Globe News Wire, it is predicted to reach $425 billion by 2027.
Internet of Things (IoT)
This innovative technology embodies the connection of devices with the internet infrastructure. Having this type of solution can help manufacturers like you make informed decisions with the help of the data provided.
It also lets you create strategies that involve cost reduction, adds more innovation, and enhance safety. Research showed that almost 31% of production processes currently incorporate devices and integrate intelligence. On the other hand, 34% of the respondents plan to incorporate this technology, and 32% plan to have IoT in the products.
The numbers show that this trend is growing! Having this solution can let you safely monitor equipment and detect its possible issues. These features look like it’s time to consider having IoT strategies for your business.
Predictive Analytics and Predictive Maintenance
Are you thinking about keeping your production on track? Then it’s time to consider having predictive maintenance for your company!
This trend helps you and your team lessen outages and prolong the machinery life. Having predictive analytics makes it easier for manufacturers to monitor equipment and its performance through using metrics. They can also gather the data collection process through IoT tools.
It lets you receive insights to have a better understanding of how your systems function and know when they will fail. Predictive analytics can help your team save resources, time, and money.
Back-to-work strategy
Getting ready for the post-pandemic work setup is something to consider. However, the transition must be safe, and it should still follow the protocols. You should also remember that in getting back to the office, working will not be the same.
Your business has to be more resilient and better equipped if the next crisis arrives. If you’re thinking about bringing your team back to the warehouse or office, then you need to have a plan for making the environment safer for them.
Luckily, there are platforms like Salesforce Work.com to help you and your team go back to work safely. In this “new normal”, this feature has apps, resources, and solutions that help businesses reopen safely. To know more about this platform, read this article here.
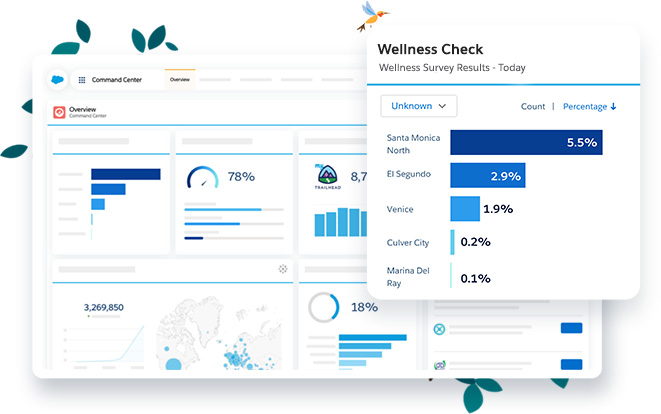
Leveling-up enterprise resource planning (ERP)
ERP systems help manufacturing companies streamline processes through automation. It also helps them provide accurate data and reduce costs.
The COVID-19 pandemic has changed the way they use ERP systems. To use it to its full potential, you can have a cloud-based solution so that your team has access to the systems wherever they go. Using a cloud-based system can help you and your staff have productivity at work, despite the distance.
Expanding data
The more your company grows, the more data will be there from various sources. For the manufacturing industry, that means companies have to invest in cloud computing software that makes it possible for them to access data, and at the same time, simply work on a successful remote working or back to the office setup.
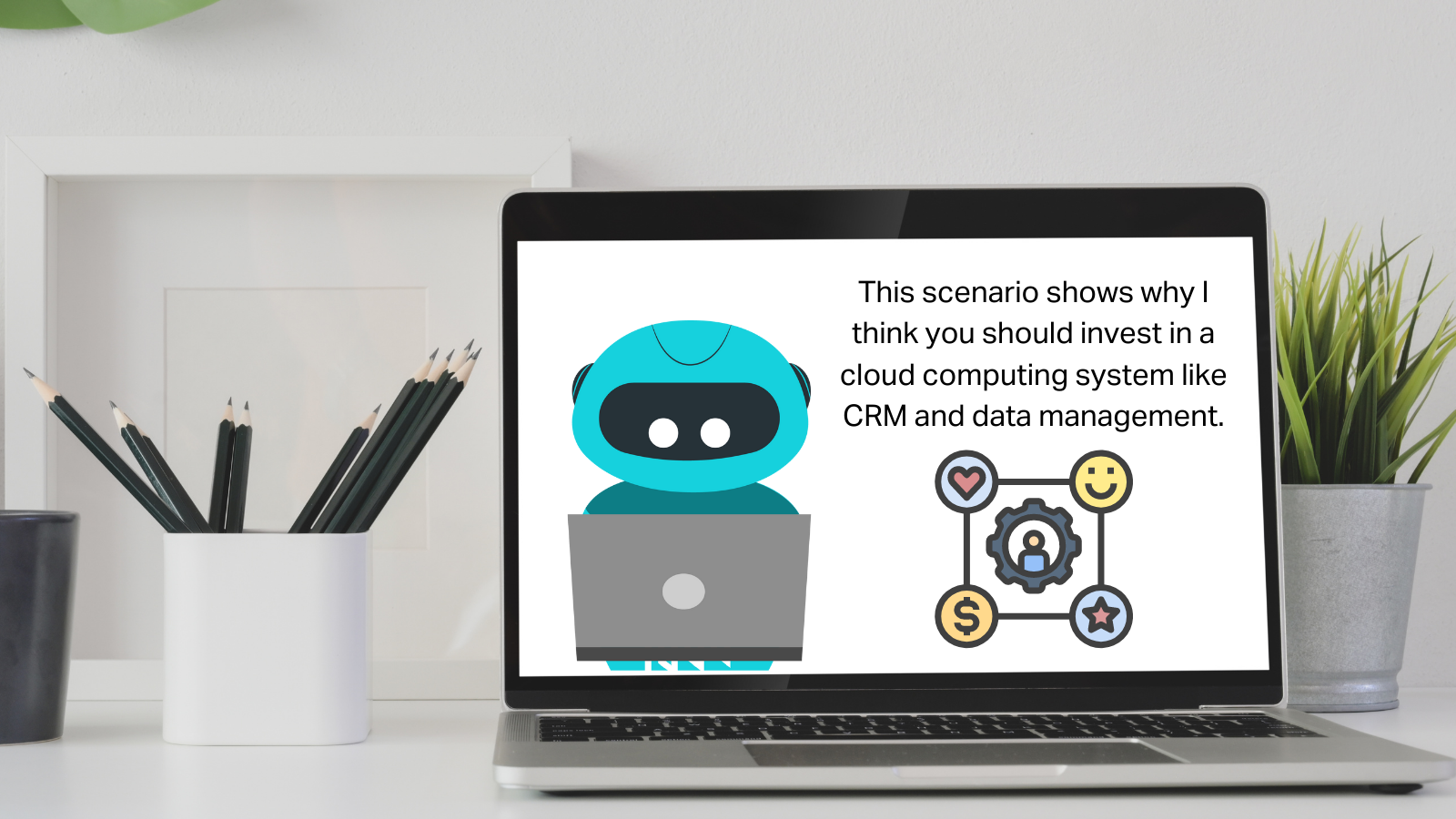
Virtual Reality (VR) and Augmented Reality (AR)
The pandemic hindered manufacturers from going to their work to add equipment or fix damaged products. But wait… There is a bright side to these difficulties! These technologies allowed workers like technicians to have assistance to their customers by sending them VR and AR devices and guiding them through what was going wrong.
Another advantage of using this technology is that it gives security and quality. A Smart Tek article mentioned that it brings increased security since it helps spot and avoid threats, guides employees, and lessens the chances of accidents. What makes it beneficial is that it ensures a better quality of manufactured goods and quick time-to-market.
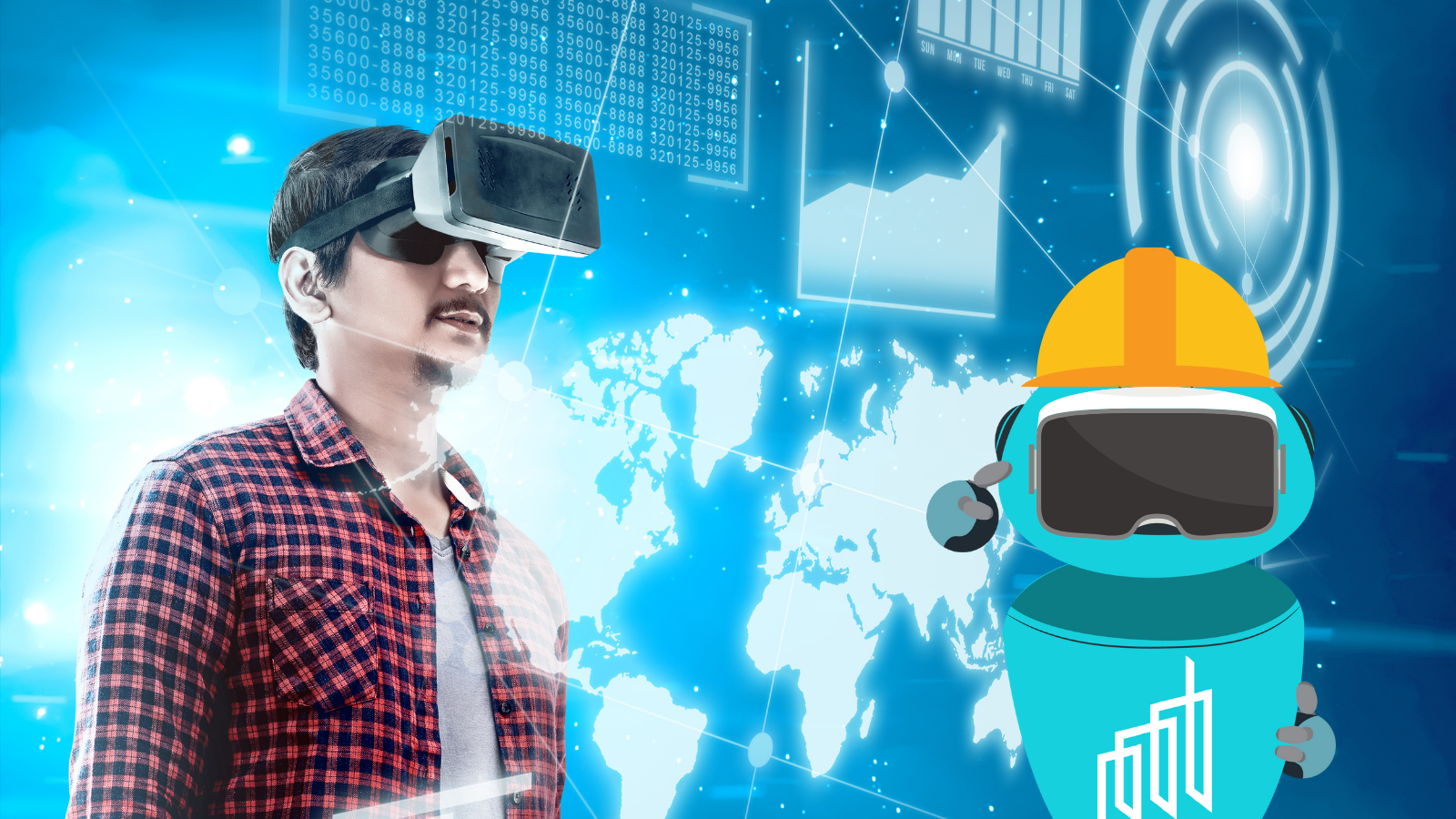
Amidst the obstacles, innovation always paves the way for growth! I know that you, as a manufacturer, deserve the technology that helps your business stay resilient and continue growing despite the current circumstances.
Bouncing back from what your company went through is always possible. With the right technology, I’m sure that you and your team will keep the products flowing as the customer demands change over time.
Are you deciding on what is the right tech solution for your company? Our team at Third Pillar is here to answer that question!
Download the ebook here to know more about Third Pillar and its Salesforce solutions! You can also read the other customer success story on our Service Cloud implementation.
To understand more about our CRM services, chat with us here so that we can discuss the right solutions for your business.
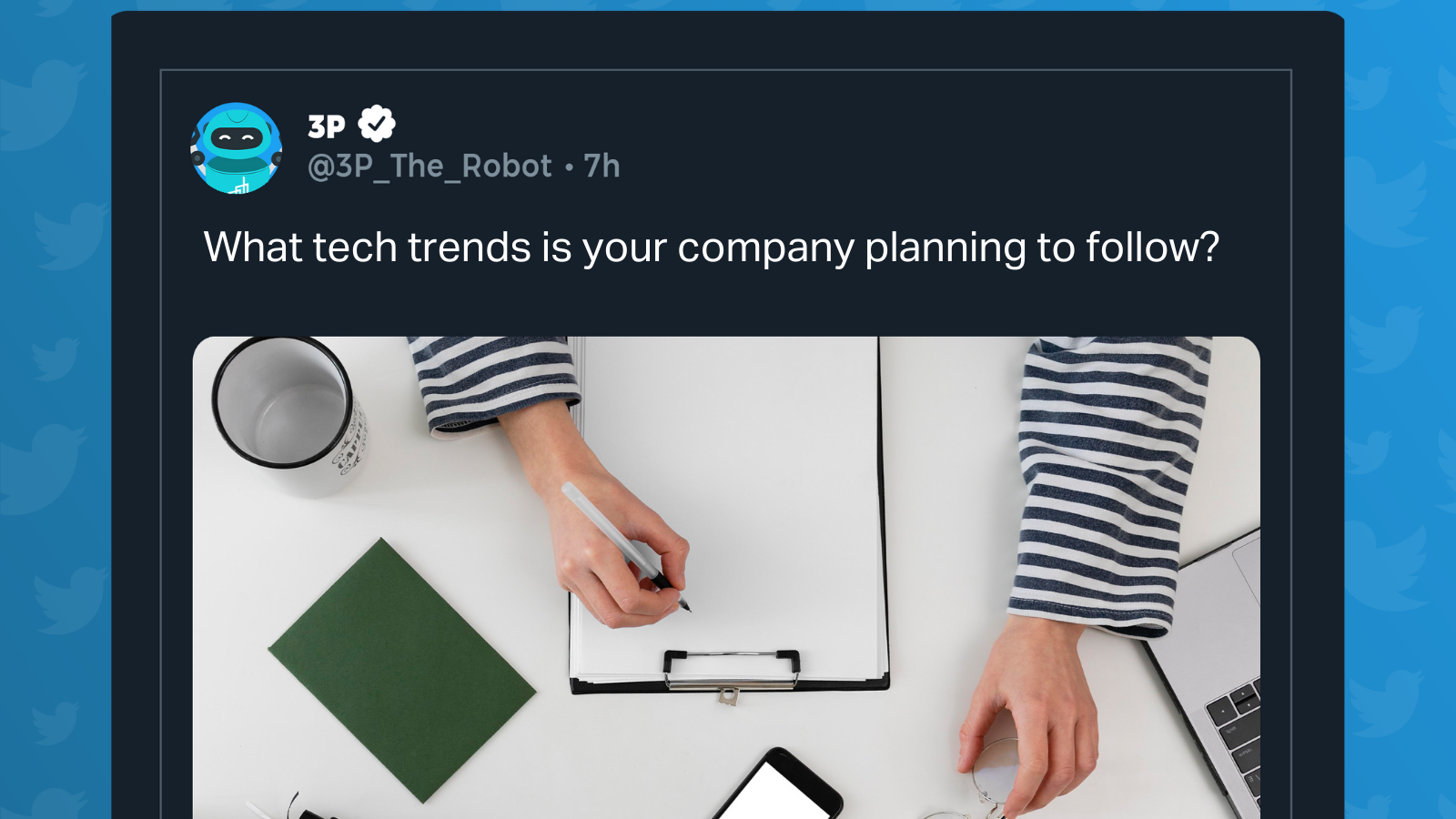